In three different projects we have worked to reduce the amount of water used, in production, in formulation and in use. This is essential for us to reduce the environmental footprint from our consumption and life.
In production: concentrated and yet processable leads to cost savings!
Reducing the amount of water in concentrates used in production processes can save much in terms of shipping, space and packaging materials. What needs to be remembered though is that this concentrate still needs to be possible to work with, for example to be pumped through pipes or sprayed through nozzles. In one project the aim was to enable the maximum concentration of surfactant with retained low viscosity. All working with surfactants knows that there will be limits to this, based on the structures formed by the material at high concentrations.
Our approach was to produce phase maps to guide the client to the formulation window and how surfactant parameters such as chain length and polydispersity as well as co-solvent additions will determine the maximum surfactant concentration. This led to cost savings at the plant!
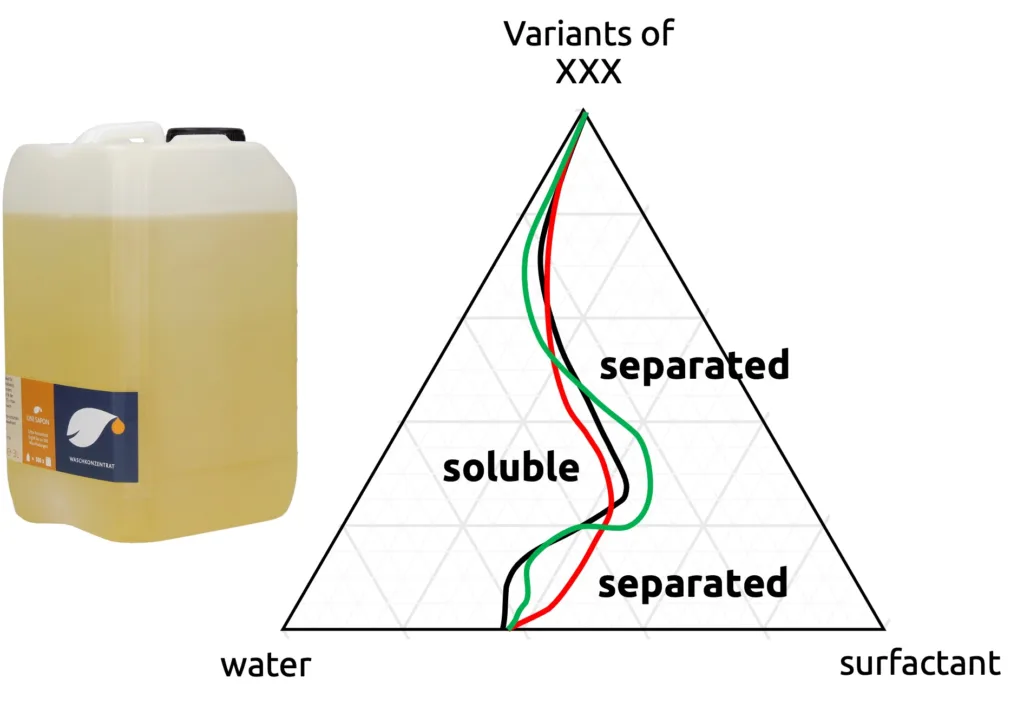
A phase map depicts how samples with different compositions appear.
Here, it was non-intuitive that a higher concentration of surfactant could be achieved and still have a solution possible to process, with a small addition of XXX. Other phase maps can show borders between areas where samples are very viscous or have liquid crystalline character for example. Very useful.
In products: just add water, if kinetics is on your side
Many ask themselves, why cannot I add the water at home, in my shower or sink, instead of the products containing so much water? I don’t want to pay for water! I don’t need water to be transported over the globe!
Well, many are in fact working on such products, but it is far, far from trivial with retained performance and user experience. It becomes critical to find a combination of cleaning agents (surfactants), conditioning agents (polymers) and other wanted ingredients that can not only form a nice dry solid shape but also dissolve quickly and evenly, foam as much (shower) or little (laundry) as wanted and releases whatever other nice actives (perfumes, oils or caring substances) in a homogeneous way. This is far, far from trivial. Our job has been to look at this compatibility of ingredients to guide the developers to which combination is most viable. This combination is thereafter used as the platform system from which, several products with different applications are made. Yes, once again a phase map saved time and money.
In use: whatever water is used – re-use it!
What if we started to look at used water as a source for another process or product?
It could be an even better solvent, a smart rinse aid or a more nutritious water for our plants. Indeed, there are shower producers who have smart constructions for letting us re-use our water in-use, reducing the consumption with magnitudes! And there are consortia that are in it for the big change: having us in the rich countries consume only 10% of today’s volume in our homes. Check out #50Lhome – the Coalition spearheaded by P&G that aims to make 50L per person per day feel like 500L, at 0 carbon… To this point, we have been lucky to start pioneering possibilities with P&G and several other companies – leading deep-dive characterisation work of the used “waste” water to help inform how it can be filtered, treated and eventually re-used with retained or even enhanced performance and consumer appreciation.
This is a topic extremely close to our hearts – if you have a project, product or process that could be made better through smarter water usage – please get in contact!
Illustration by Maja Stenstam