A life-saving medical device, used in hospital ICU:s in the urgent situation of sepsis. The product is well-established on the market, and production is routine. What could CR possibly bring to the table? With high ambitions to expand the product portfolio and target new indications, the management of Alteco Medical engaged us to collaborate in the product development process. Starting the partnership, it was decided to investigate the present product and manufacturing processes first, enabling a deeper understanding to benefit the next part of the assignment. The possibility to improve current production efficiency was evaluated in parallel, as an added benefit. We call this “Fast forward by looking back”.
Calculations to underpin the potential
This project series started with in-depth conversations with our client to fully map any knowledge gaps regarding their product and evaluate the production process steps to find the greatest improvement potential. The cost of key materials and the process time were identified as the two key factors, as both were strongly related to the manufacturing efficiency and total production cost. Could the amount of expensive chemicals used in the production process be reduced? Based on the molecular size, initial theoretical calculations were made on the amount of a certain molecule that could bind onto the available surface area. Indeed, these calculations indicated that the expensive chemicals were used in significant excess! As we know that theoretical calculations sometimes do not correlate with actual reality, the next step was to verify these results in the lab.
Process optimization and analytical development
Our most creative colleagues started by implementing a lab-scale version of the production. This miniature setup allowed for continuous monitoring of UV-active chemical concentrations through a connected UV flow cell. What was initially thought to be a straight-forward process turned out to be more complex, requiring method development and evaluation of several techniques before obtaining reliable data. Ultimately, UV spectroscopy, NMR, and HPLC was used to measure the concentration of the chemicals at the start and end of the lab-scale production process. The results confirmed that there is great potential to optimize and streamline the production process
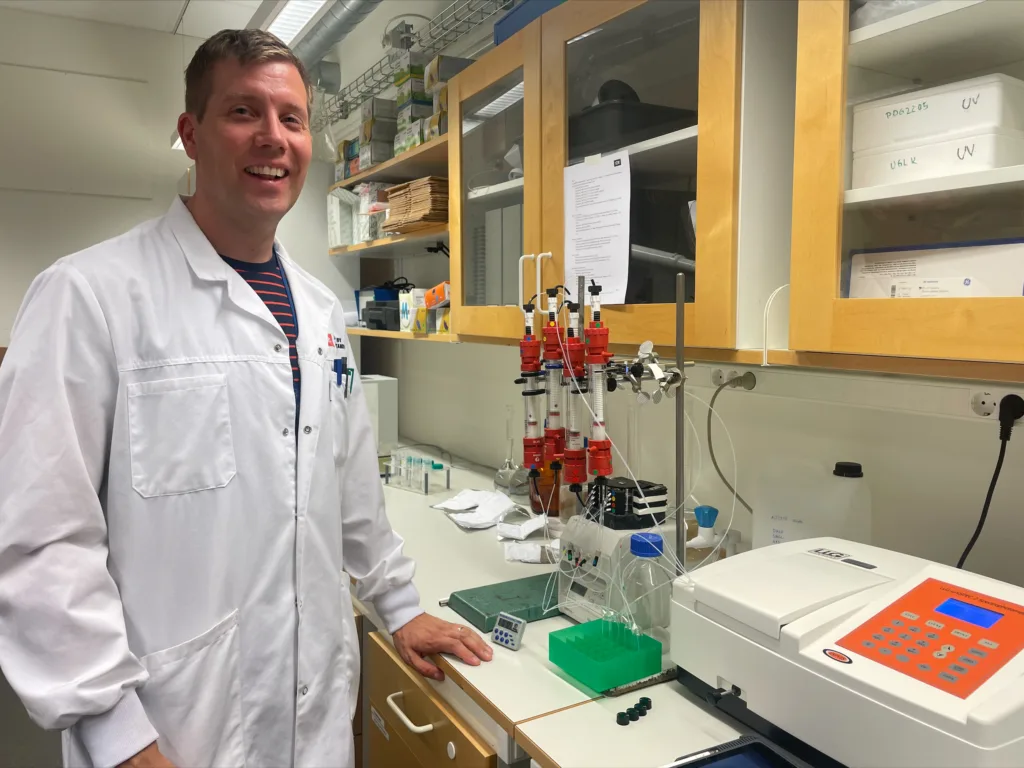
Henrik Almqvist by the down-scaled set-up with on-line UV analysis, for optimization of the production process.
The Deliverables and Next Steps
The project outcome demonstrated strong support for potential cost and time reductions in the current production process, while our tailor-made analytical methods can be used by the customer in upcoming product development as well as subsequent quality assurance procedures. In addition, having a lab-scale process up and running means we are prepared for further product development collaboration with Alteco Medical.
The next step is to further optimise the production process by evaluating lower chemical concentrations and processing times while, of course, maintaining the high quality and efficacy of the device. We call this “Quality by Understanding”.
We saw exciting potential in our new product but needed external competence to benchmark our product development.
MD Fredrik Jonsson, Alteco Medical AB
CR made us realize we could explore the potential to streamline our existing production process at the same time.